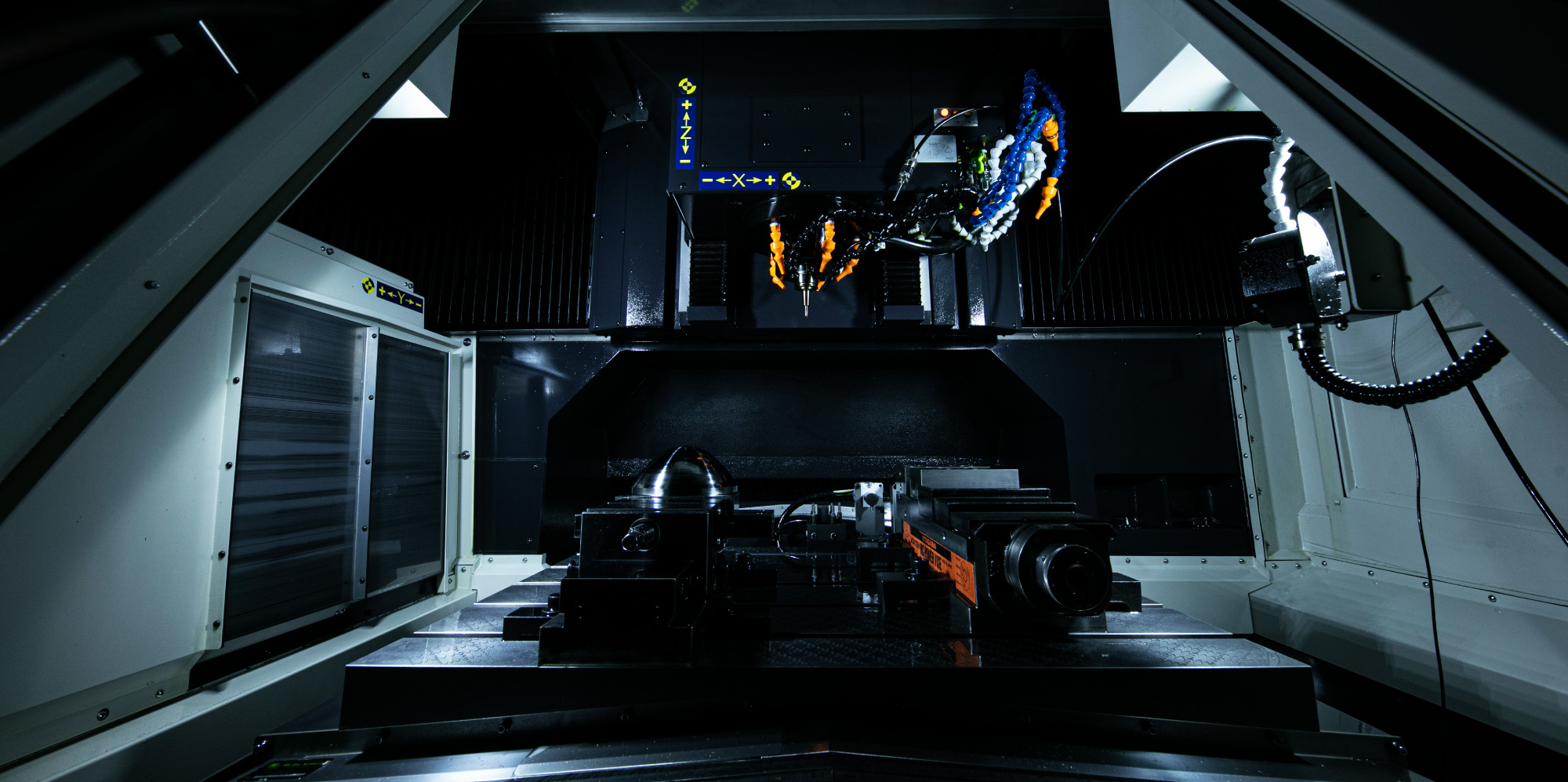
It has been more than 20 years since the astounding debut of this series
MEGA micro machining centers have constantly evolved to meet the needs of the era, leading the field of micro machining.
The latest technology is now integrated into the standard model, pride of the company
The culmination of ceaseless evolution
… 6th Stage [MEGA-SSS]
Axle Movement (XYZ): | 410 / 330 / 200 mm |
Spindle Speed: | 3,000 – 40,000 rpm (SSS-400) 3,000 – 60,000 rpm (SSS-600) |
Spindle End Format: | 1/10 short taper (two-sided restraint) |
Tool Shank Format: | HSK-E25 |
ATC Tool Storage Capacity: | 20 tools (OP: 40 tools / 60 / 100 tools) |
Machine Weight: | 2,600kg |
Along with other features, this stimulates the senses of the operator
5-axes control specifications that realize the ultimate integration of XYZ high-precision 3-axes positioning capability and added 2-axes indexing precision
Exclusive design simultaneous five-axis control that comes standard with scale feedback on both the tilt axis and rotation axis
AHC [Specifications 1] | AHC [Specifications 2] | APC [Specifications 1] | APC [Specifications 2] | |
Work Stocks: | 24 / 40 / 60 units | 10 units | 33 surfaces | 45 surfaces |
Max Dimensions of Carried Object [W x D (mm)]: | 70×70 | 230 ×230 | 200 × 190 | 100 × 120 |
Max Dimensions of Carried Object [With nothing adjacent (mm)]: |
70 × 130 | 230 × 230 | ― | ― |
Max Height of Carried Object (mm): | 130 (including holder height)) | 130 (including holder height) | 150 (including pallet height) | 130 (including pallet height) |
Max Weight of Carried Object (kg) | 5 (including holder) | 20 (including holder) | 20 (including pallets) | 10 (including pallets) |