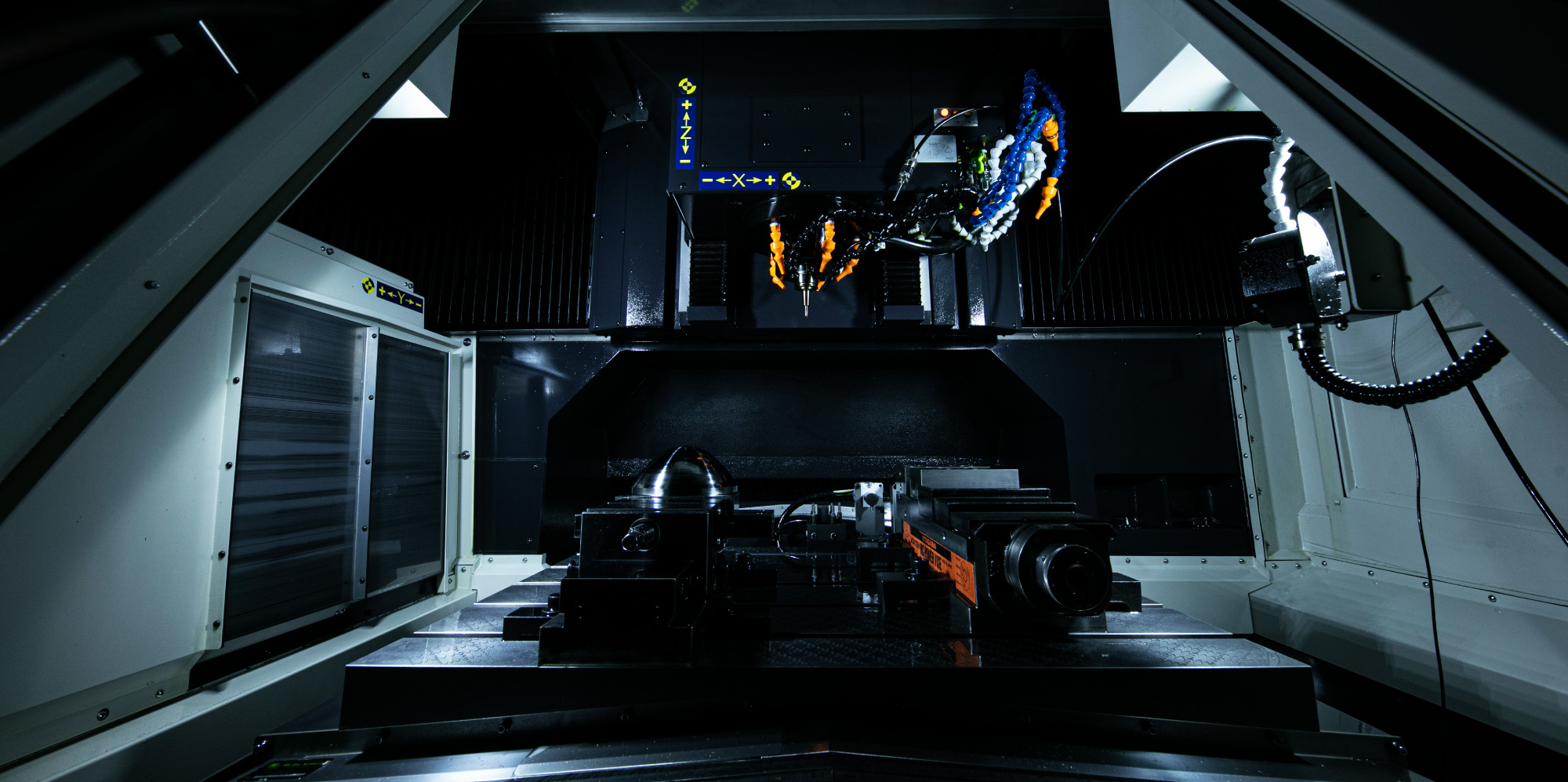
Android was originally developed based on the concept of “pursuing real machining precision of ±1 μm”. We have reduced displacement as much as possible and made improvements to achieve higher precision machining, even in high speed machining conditions. These brush-ups have resulted in a next-generation model of Android that meets higher level demands from our customers. We have named it the “Android II Ultra High-Precision High-Speed Micro Machining Center”
Axle Movement (XYZ) | 450 / 350 / 200mm |
Spindle Speed | 3,000 - 60,000 rpm |
Spindle Taper Hole | 1/10 short taper (2-sided restraint) |
Tool Shank Format | HSK-E25 |
ATC Tool Storage Capacity | 20tools (OP: 40 / 60 / 100 tools) |
Machine Weight | 5,800kg |
■ Evolution of Android
◆ Higher precision
・Stronger measures against thermal displacement (Active H.I.S.)
1. Strengthening measures for heat exhaust
By improving ventilation efficiency around linear motors of the main spindle and each axis (X, Y, Z axes), it reduces thermal displacement in the Y-axis direction
2. Guide part carriage cooling
Maintains high precision for long periods of time by cooling the guide part, which is a source of heat
*Active H.I.S.: Active Heat Isolation System
■ Evolution of visualization
◆ Evolution of M-Kit
1. Measurement Points: 16
2. Uses Touch Panel logger
◆ ASC Function
Automatically detects saturation of the spindle
Reduces warm-up time and shortens non-machining time
* “ASC Function”: Auto Saturation Check
This machine has specially engineered simultaneous five-axis control specifications, which promise ultra high-precision machining, thanks to the Android II’s XYZ 3-axes positioning capabilities and extremely small thermal displacement.This machine has specially engineered simultaneous five-axis control specifications, which promise ultra high-precision machining, thanks to the Android II’s XYZ 3-axes positioning capabilities and extremely small thermal displacement.
Supports multiple applications, including ultra high-precision dies, medical, optical, and electronic device part processing.
AHC [Specifications 1] | AHC [Specifications 2] | |
Work Stocks: | 24 / 40 / 60 units | 10 units |
Max Dimensions of Carried Object [W x D (mm)]: | 70 x 70 | 230 x 230 |
Max Dimensions of Carried Object [With nothing adjacent (mm)]: | 70 x 130 | 230 x 230 |
Max Height of Carried Object (mm): | 130 (including holder height) | 130 (including holder height) |
Max Weight of Carried Object (kg): | 5 (including holder) | 20 (including holder) |