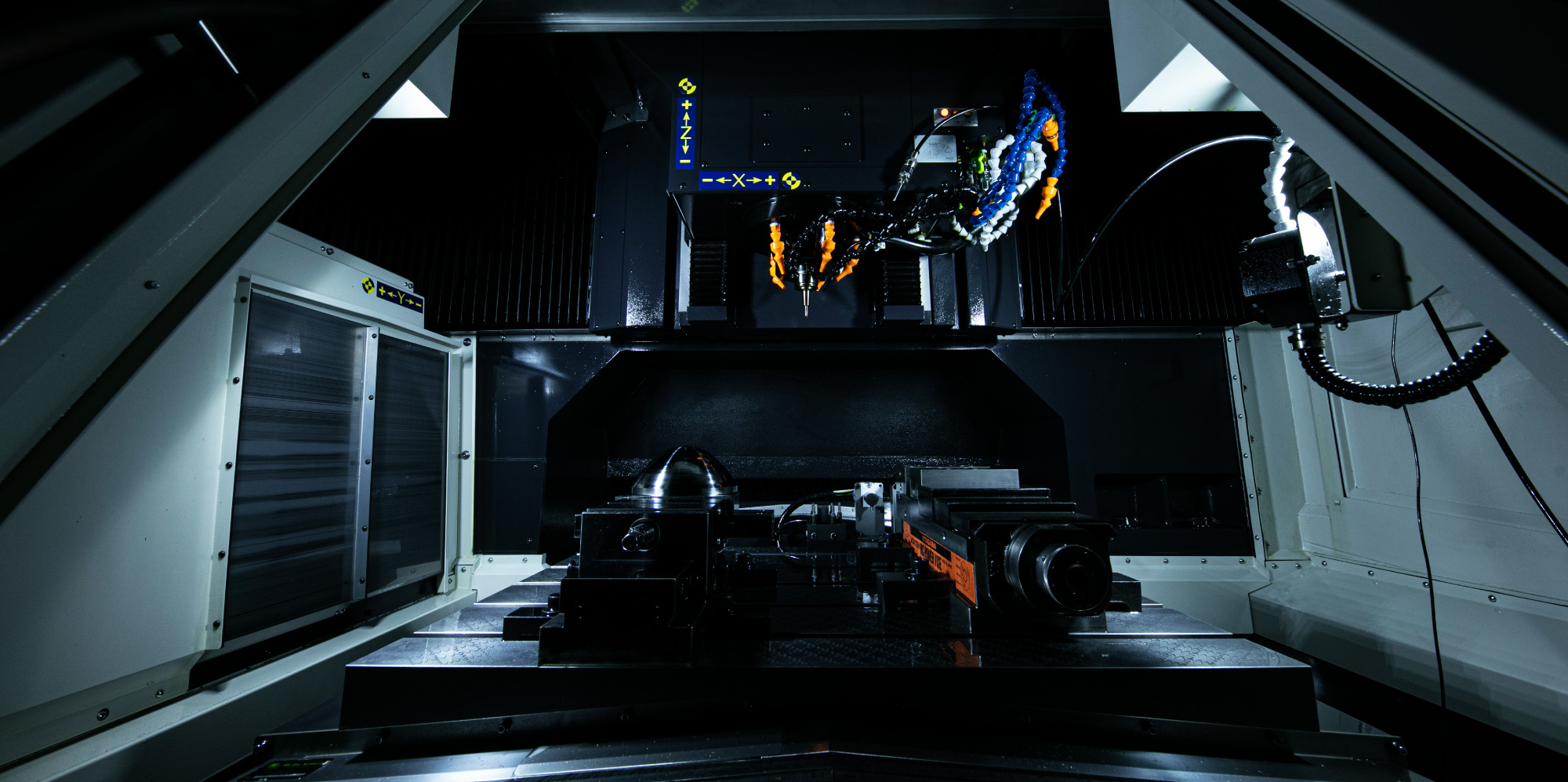
1/2/6-Axes Lineup
Achieved actual machining precision of ±0.030
Σ-621R | |
Number of Spindles: | 6 |
Axle Movement (XYZ): | 690 / 540 / 70 mm |
Spindle Speed: | 5,000 – 60,000 rpm (OP: 20,000 – 80,000 rpm / 5,000 – 40,000 rpm) |
Machine External Dimensions: | 4,265 × 2,090 × 1,900 mm |
Machine Weight: | 8,600kg |
Σ-220R | |
Number of Spindles: | 2 |
Axle Movement (XYZ): | 630 / 520 / 70 mm |
Spindle Speed: | 5,000 – 60,000 rpm (OP: 20,000 – 80,000 rpm / 5,000 – 40,000 rpm) |
Machine External Dimensions: | 2,135 × 1,885 × 1,900 mm |
Machine Weight: | 2,550kg |
Σ-120R | |
Number of Spindles: | 1 |
Axle Movement (XYZ): | 630 / 520 / 70 mm |
Spindle Speed: | 5,000 – 60,000 rpm (OP: 20,000 – 80,000 rpm / 5,000 – 40,000 rpm) |
Machine External Dimensions: | 1,390 × 1,750 × 1,580 mm |
Machine Weight: | 1,950kg |
Comes equipped with a machining program drawing function. This enables Comes equipped with a machining program drawing function. This enables checking drawing of the machining progress status, as well as restarting the program, and doing direct format conversion. A wealth of functions needed on site are available.
1) Machining Status Screen
Displays information about tools being used and programs that are running. Check the machining status at a glance, including the progress of machining.
2) File Management Screen
This screen is for selecting machining programs and managing files. The Windows format makes it easy to understand, in order to easily copy, edit, and delete files.
3) Drawing Screen
This screen draws and displays the selected machining program. When a tool is broken, the program can be restarted by clicking directly from this drawing screen. It is also possible to convert program formats with a simple operation, making it easy to convert to our format and make version settings.
[Option] Machining Range Setting Function
This function makes it possible to set the range for the part you want to machine on the drawing screen, in order to extract a program for that part. This makes it possible to easily do partial machining and restoration.
4) Cutting Conditions Screen
This screen is for editing cutting conditions. Editing can be done while referring to the program. It is also possible to easily extract cutting conditions by registering cutting conditions in a data bank in advance. Furthermore, it is possible to set deep drilling cycles for each tool diameter.
[Options]
● K-Function
This function registers the amount of wear on tool diameter according to cutting length in advance, so that corrections according to the cutting length can be set automatically during operation. It is possible to continue machining without worrying about tool diameter wear, thereby improving productivity and realizing high-precision machining.
The optical sensor constantly monitors tools that are currently being used to do machining. When a tool breaks, it stops the machining center and displays the broken part on screen. This enables quick recovery work, promising benefits such as improved productivity and reduced rate of defects.
*Only supports pressure foot for inner pin machining
The board fixed in place with a stack pin can be quickly and easily removed. Removing the board in a shorter time helps increase productivity. A single unit is compatible with both the method of pulling down the stack pin and the method of pushing up the board.
By combining a pressure foot with software, we have realized external dimensional accuracy of ±0.03 mm with a small workpiece 10 x 15 mm (actual results under conditions at Roku-Roku).
Inside Square: Actual size of
10 x 15 mm